Traditionally, the food industry has used spirals built with metal conveyor belts. But, with the passage of time, these belts suffer from wear and deformation, which, when they need to be replaced or repaired, require time, impacting directly on the production line. In order to overcome these disadvantages, we resorted to the use of a belt with the longest useful life for the manufacture of our spirals, highly hygienic, that does not accumulate bacteria during the process and at the same time does not cause unexpected stops, with the objective of improving the production of our users. Intralox developed an innovative system of plastic belts for spirals, which allows unique configurations obtaining, as mentioned, benefits both for the products and the production line.
During food processing, conveyor belts play a fundamental role, since any impact on them can mean lost production hours. As we mentioned, plastic belts solve certain inconveniences compared to metal belts, thanks to the benefits they provide:
- Hygiene. They are characterized by their ease of cleaning. Mainly due to the design (since there are no dead spots for the accumulation of residues) due to the nature of the materials with which they are built. Under the same cleaning conditions, it has been proven that it is common to find pieces of food or residues on the metal belts.
- Improvements in production. Given the characteristics of plastic belts, they do not require lubrication, since the friction and tension they present are significantly lower than those of metal belts. This not only improves production times, but also, and linked to hygiene, eliminates the metallic residues generated by metal belts, which are usually lodged in the products. At the same time, its low noise level contributes to reducing noise pollution in the plant.
- Improved product quality. Metal belts, made of thin wires, generate an irregular support surface, causing the product to be supported unevenly. On the contrary, plastic belts generate a smooth surface, which translates into better product support, elimination of marks and reduction of product damage, as well as less adherence of the product to the belt, making it easier to remove.
- Prolonged service life. One of the great advantages of plastic belts has to do with the memory of plastic as a material, which allows the belt to recover its original shape after moving back and forth as it works in a spiral. On the other hand, metallic belts suffer from metal fatigue, which causes deformation and breakage of the belt with use, requiring more frequent replacement or repair.
- Ease of repair. We know what a headache it is to repair a metal conveyor belt, because of the stoppage it generates in the production line. On this point, plastic belts present another enormous advantage. As they are modular belts, at the time of a repair, the affected section is simply identified, and by removing a single rod, a non-destructive repair can be made in a matter of minutes.
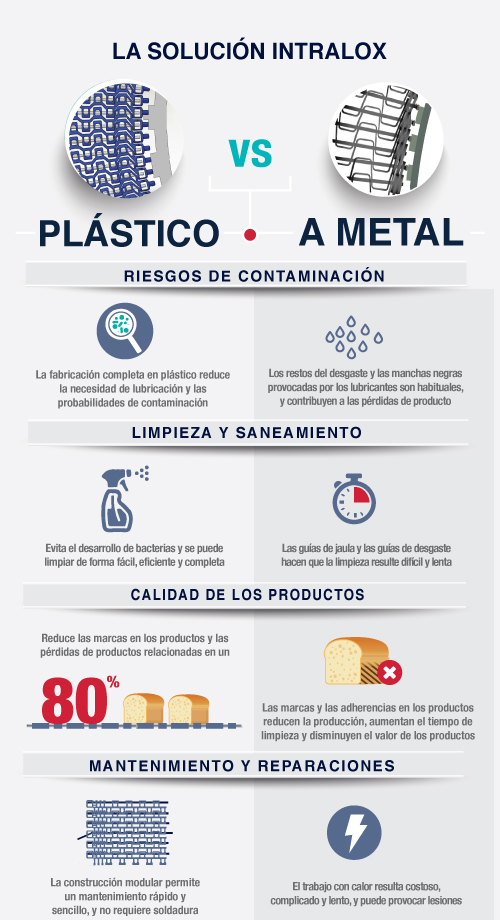
In Abreu we have an engineering team that works together with each client, advising them in order to develop the machinery that meets their specifications and needs, maximizing the production performance and, at the same time, optimizing the floor space in the plant.
If you have any questions, we invite you to contact us.